Loadout Management System: LOADRITE 360 for Loadout
LOADRITE 360 is a connected quarry solution that can holistically improve loadout operation through performance metric tracking, job data automation, and real-time 360º job visibility.
LR360 connects the loader and scale house to provide data sharing of loadout jobs which result in greater efficiency, improved visibility and higher product sales.
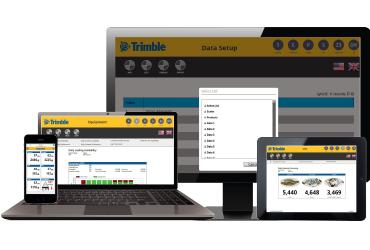
InsightHQ connection
LR360 performance reports tracks loader metrics including tonnes per hour (TPH) across multiple or individual loaders, actual time spent on truck loading activities and loader operator efficiency to highlight staff training needs.
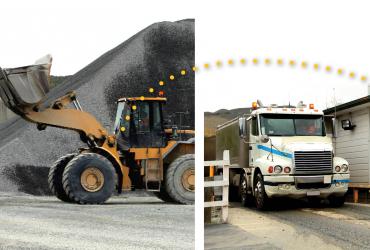
POS system and in-cab automated connection
Two-way automated communication shows jobs requested at the scale house as a job list inside the cab, and completed loadout data is fed directly into the scale house POS. This reduces double entry work and data entry errors for both the operator and scale house attendant. Accurate on-screen job data reduces error-prone verbal comms chatter, and allows more time for loading.
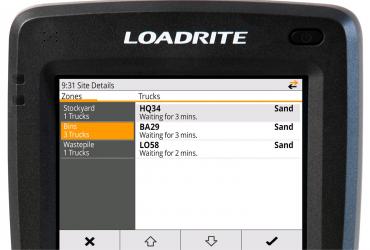
Real-time job list
The LR360 in-cab indicator clearly presents a list of loadout jobs in order of priority and the truck ID. By providing simple, relevant and organised job data to the operator they are empowered to deliver faster with a sense of urgency and priority across the site. The list also provides richer load out job queue data, reduces verbal communication, and errors, which reduces truck waiting time and happier customers.
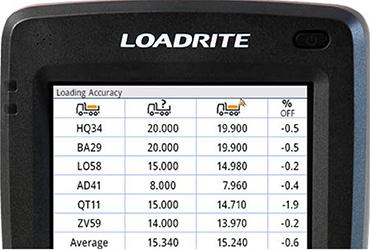
True tare trucking loading
The truck and payload is measured three times for each loadout: upon arrival at the truck scale (weigh bridge), at loadout on the loader scale and true payload is verified on departure. True truck payload measurement maximizes tonnage and optimizes truck utilization for the customer and maximizes product sales at the scale house.
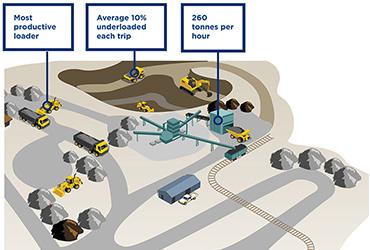
How it works
LR360 decreases rework and miscommunication by wirelessly synchronizing data between the loader and the scaleshouse.
- As the empty truck arrives its weight is recorded and material request data entered into the POS.
- The job details are wirelessly transmitted to the loader and displayed in the cab in a prioritized list.
- When the job reaches the top of the list, the loader operator can go to the material, identify the truck from the ID and load precisely to the target weight.
- At the completion of the job, the data is returned to the scale house and billing is automatically adjusted before the truck arrives to tare out.
- The quarry manager is able to see loadout operations in real-time with a clear view of workload, productivity and performance.